液状シリコーン射出成形を実現する、超精密金型について
※この原稿は、当社が月間プラスチックに執筆した現行を掲載したものです。
1. はじめに
わが国では、液状シリコーンゴムは約20年前に導入され、一旦は市場拡大されると思われたが、成形技術や金型の未熟さが主たる要因で、その伸びは鈍化し停滞してしまった。しかし、近年では液状シリコーンゴムのもつ優れた耐熱性や耐寒性、耐薬品性が市場で再認識され、熱可塑性プラスチックのエラストマー樹脂の上を行く材料として精密機械や家電、OA、医療、自動車業界などで順調に市場が拡大している。その要因として、以下の事が考えられる。
- ①射出成形機と2液混合装置の性能がアップ
- 材料が液状であることから計量精度と吐出精度が確保され、製品にショートショットやバリが発生しにくくなり、製品精度が良くなった。
- ②金型の加工技術のレベルアップ
- CAD/CAM,工作機械の高精度化により、高精度金型技術が進化した。また、熱膨張を含めた温度分布や温度管理への認識と、エアー抜き加工技術、コーティング加工技術等の温度と脱型に係る意識が高まった。
- ③液状シリコーンゴム材料メーカの材料開発
- プライマーレス液状シリコーンゴム材料の出現でプラスチック部品との接合が容易になった。プラスチックと液状シリコーンゴムとの2色成形、インサート成形が可能になり、高付加価値製品への応用展開や工数削減とハイサイクル成形の実現で生産コストダウンが可能となった。
2. 液状シリコーン射出成形金型の意義
2-1シリコーンゴムの優位性
シリコーンゴムの優れた特徴として、以下の点があげられる。
- ①耐熱性、耐寒性に優れる
- ②人体に優しい
- ③電気絶縁性に優れる
- ④着色性に優れる
- ⑤耐水性に優れる
- ⑥耐油性に優れる
- ⑦耐薬品性に優れる
この様な特徴を生かして、精密機械や家電、OA、医療、食品、スポーツ用品等、多くの物に使用されている。
2-2液状シリコーン射出成形を実現するメリット
プラスチック製品は主に射出成形で生産され、ロボット、カメラ等を使用して無人化が進んでいる。
一方で、プラスチックに比べて液状シリコーンは粘度が低いため、金型のクリアランス(10μ~20μ)の間にシリコーンが流れ込んでしまう。そのため、バリの発生、離型が難しく、実際に無人化で成形しているメーカーは数少ない。
そのような理由から、一般的にシリコーン製品は、ミラブル型シリコーンを使用した直圧成形で成形されることが多い。直圧成形では、材料を正確に計量できず、バリが大量に発生するため材料ロスが大きくなる。また、製品の離型は作業者が行う上に、材料の特性上硬化時間が長く生産効率が悪い。
したがって、液状シリコーンゴムの成形を射出成形で行う意義は大きい。
今回は、液状シリコーンゴムの射出成形を実現するための金型加工技術にポイントをおき、弊社で製作した試作金型の特徴と検証結果および今後の展望について述べる。
3. 試作金型の製作
3-1製品設計
今回、試作でトライする製品は、「シリコーングラス」とした。理由は以下の通りである。
- ①寸法サイズ
- 成形機の対応可能サイズの関係上、小型の製品にする必要があったこと。
- ②離型性
- 離型性を確認するため、平たい形状ではなく立ち上がりのある形状とする必要があったこと。
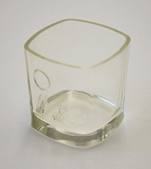
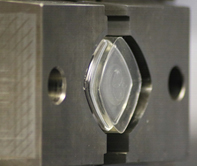
3-2全体構造
今回の試作金型の全体構造は図の通りである。
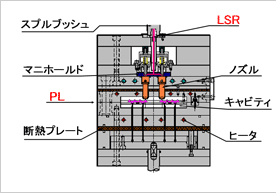
設計のポイントは以下に記す。
3-3コールドランナーシステムの採用
一般的な射出成形金型では、スプール、ランナーが必要である。
液状シリコーンは、材料費が高価で硬化後の再利用が不可能なため、廃棄に係る費用も発生する。
また、ゲート処理や製品とスプールランナーの分類工程が必要となる。
そこで、今回の試作金型では、フィーサ社のコールドランナーシステムを採用した。
コールドランナーシステムを採用する事により、以下の事が改善された。
- ①材料が100%製品になるため、材料の歩留まりが良い。
- ②産業廃棄物も激減するため、環境にも優しい。
- ③成形サイクルが短縮できる。
- ④製品のみを取り出せば良いため、成形の自動化も図りやすい。
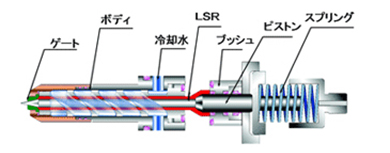
3-4スライド構造の採用(バリ検証のため)
今回の試作金型では、液状シリコーンの射出成形においてより厳しい成形条件とするために、「スライド構造」を採用した。
一般的に、プラスチックの射出成形では、スライド構造は抵抗なく採用されている。
ただし、液状シリコーンゴムは、粘度が低いためスライドのクリアランス(10μ~20μ)の間に流れ込んでしまいバリの発生に繋がりやすい。
今回は、あえてスライド構造を採用することで、バリについて検証しやすくする目的があった。
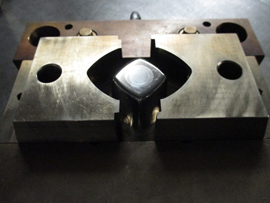
4. 結果検証
4-1使用成形機
今回のトライでは、成形機として「ソディックLSR40A」を導入した。
液状シリコーンの射出成形では、正確な計量性能が求められるため、射出プランジャと可塑化スクリュを独立させたソディックのVライン機構が最適と考えたからである。
なおかつ、液状シリコーン専用射出成形機として、「ソディックLSR40A」を採用した。
2色混合装置は、「DOPAG SILCO-MIX」を使用した。
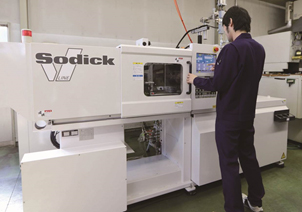
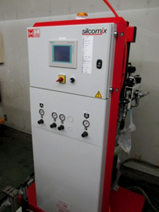
4-2金型表面の加工精度とバリとの相関関係
金型の表面粗さとバリの発生との相関関係について検証した。
マイクロスコープで製品のバリ表面の拡大写真を撮影した。また、広域大段差対応白色干渉計にて金型の表面粗さを計測した。結果は、次の写真の通りである
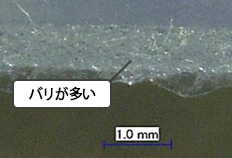
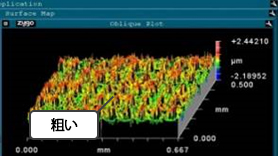
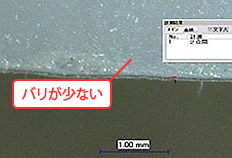
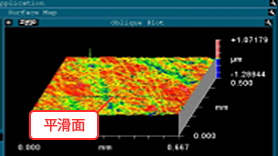
バリが0.8㎜発生した金型の表面状態は粗く、一方でバリが0.05㎜と少ない金型の表面状態は平滑であることが分かった。
金型の表面粗さとバリには相関関係があり、液状シリコーン射出成形のバリを抑えるためには、高精度な平滑面の金型を製作する必要がある。
4-3連続生産性
製品の離型させるため、今回はエアーバルブピンを採用した。初回のトライでは、離型が悪かったため、次回以降は可動側の入れ子にテフロン系のコーティング処理をした。
初回よりも、離型性は良くなったが、エアーで飛ばされると、固定側に当たり製品が傷ついてしまう。また、完全に離型せず、手とエアーを使用して製品を取る等、今回の試作では、有人で半自動が限界であった。
4-4表面意匠・バリの発生
まず、1回目のトライでは、硬度50・粘度A材680・B材640の液状シリコーンゴムを採用した。また、プラスチック金型との差を見るため、金型合わせの調整は、通常通りでトライを実施した。結果、想定していたよりもバリが発生しなかった。
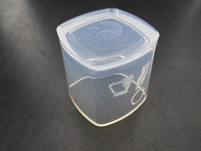
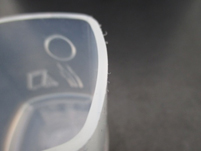
2回目のトライでは、材料のみを変更し、硬度50・粘度A材80・B材45のものを採用した。こちらでは前回の材料の約1/10の粘度となっており、トマトジュースに近い粘度の材料である。結果、想定していた通りバリが発生した。
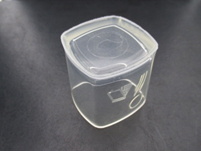
3回目のトライでは、トライ②と同様の材料を使用し、金型合わせの調整を丁寧に実施した。結果、バリの発生をかなり抑える事ができたが、金型内のガスおよびエアーの排出先が無くなり、最終充填部に気泡やショートショットが発生した。
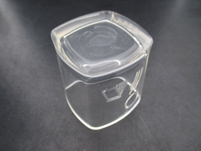
4回目のトライでは、トライ①と同様に硬度50・粘度A材680・B材640の材料に戻して実施した。さらに、スライドに5μのガスベントの加工をした。
結果、表面意匠は改善の方向に向かったが、ガスベント部に少量のバリが発生し、完璧な意匠面は得られなかった。
5. 今後の展開
5-1意匠面の改善
プラスチックの射出成形と明確に異なることは、摺動部のクリアランスからバリが発生してしまう事である。また、表面粗さとバリ発生の関係性をより詳しく追及する必要がある。さらに、ガスベントも設定しづらいため、成形圧力をかけない成形条件も必須である。
こうした点が、液状シリコーン射出成形における主要な課題である。
したがって、現時点で把握している改善点は以下の通りである。
- ①高精度な金型平滑度
- ②金型内の真空化
- ③狭い成形条件の割り出し
次回の試作では、真空ポンプで金型内を真空にして、成形条件を下げようと考えている。表面意匠で問題となった気泡、ショートの問題も解決する事に期待する。
5-2連続成産性
今回の試作では、この問題はあまり重視していなかったため、今後の展開となる。液状シリコーンが柔らかく変形しやすいため、金型の突き出し機構だけでは、離型は難しいと思われる。次回の試作では、取出機を使用し、金型+取出機の技術で連続生産性にチャレンジしたい。